Enlist Maintenance, Training, and Education to Minimize Vehicle Damage Claims at the Car Wash
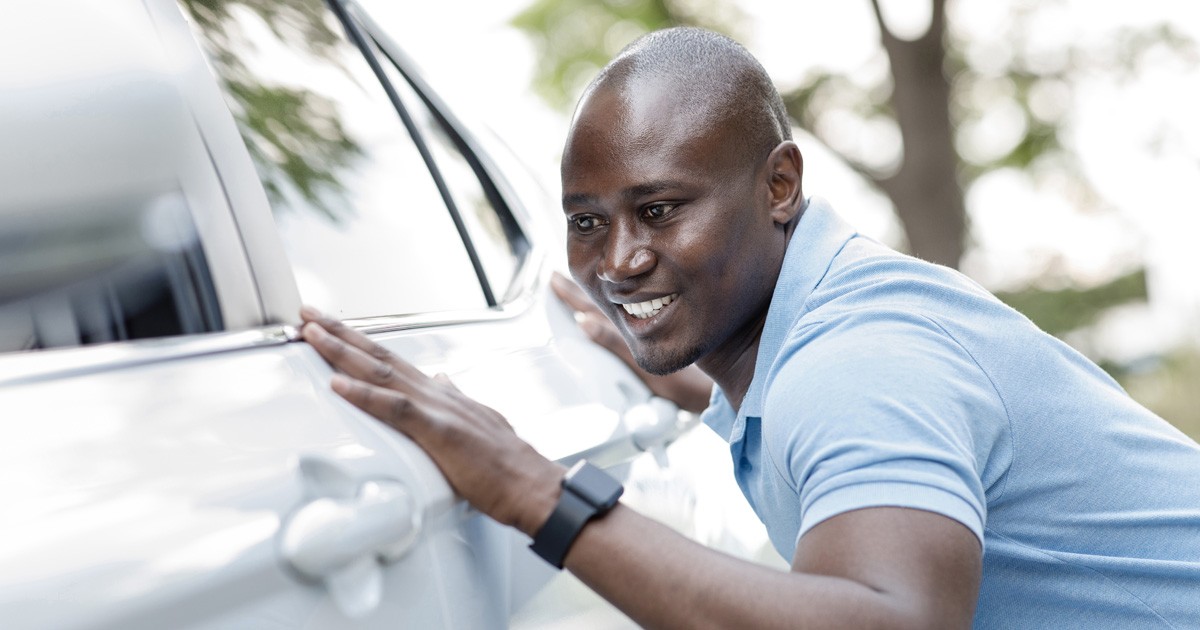
by Frank Donaldson, Service Manager / Howco Inc.
Car wash vehicle damage and the claims that follow typically have three sources: faulty or malfunctioning car wash equipment, employee error, and customer error. While damage claims are a reality of the business, there are several ways a car wash operator can reduce them significantly.
Industry standard seeks to keep damage claims between .5% - 1% of net sales. Optimally, we want no damage at all, but circumstances sometimes go awry, i.e., neglected wash equipment wears and breaks, employees don’t receive or absorb proper training, and customers don’t heed verbal and/or posted instructions and may get confused or panic. Further, some vehicles are susceptible to damage due to idiosyncrasies that make them unsuitable for certain types of car washes.
Following are some pointers and best practices that can help minimize vehicle damage at any car wash:
- Poor equipment maintenance can and will lead to vehicle damage, with costly claims following. It’s not uncommon for both new and longtime operators to overlook the value of good maintenance and preventative maintenance programs.
- To use an old maxim, the best way to prevent damage from equipment is to “nip it in the bud.” A Preventive Maintenance (PM) plan (monthly or quarterly depending on volume) with your equipment supplier is the utmost a car washer can do to catch wearing, worn, or malfunctioning equipment.
- It’s also important for the operator to observe and walk every aspect of the equipment, bay, tunnel (both sides), and lot before opening each day to watch test cars being washed and the general condition and operation of the wash facility. A well-trained employee with a keen eye and ear can often catch irregularities with a daily walk-through.
- However, a monthly or quarterly visit from your PM supplier can catch even the most subtle hints that something is or soon will be a problem. Employees conducting daily inspections might not notice small defects or issues that increase gradually each day.
- Certain aspects of the equipment need to be tested daily and should be tailored to each specific wash and type of equipment.
- The risk of unmaintained or faulty equipment is damaged vehicles; the cost of repairs; the possibility of loss of revenue via repeat business; and potential loss of reputation for the car wash business, owner, and even our industry.
- Some vehicles have preexisting damage that can be detected via camera systems that vet cars before entering and after exiting the wash. This is especially effective at high volume sites and where a wash may be unattended. Training employees to catch and point out this damage before processing a vehicle can also be key to this effort.
- Owners and operators should be educated on all aspects of wash maintenance and of potential causes of damage.
- Using personal experience, industry resources, forums, and blogs to identify problematic vehicles and trends, and subsequently educating employees on the handling of these cars, is critical with today’s quickly evolving vehicle technology.
- Use effective instructional signs and menus, as well as employee guidance where available, to clearly communicate the wash procedure with customers before they enter.
Here are items that warrant consideration to keep the car wash operating optimally:
Regular maintenance should not be ignored, as it plays a major role in preventing much damage -- anything that contacts the vehicle during the wash process has potential to cause harm. These items include:
- Brushes/cloth
- Wraps
- Top brush
- Side window washers
- Hubcap rocker panels
- Tire washers
- Drying equipment
- Dollies or pushers
- Wash volume – High volume washes wear out equipment more quickly, sometimes to the point that it doesn’t meet the standards to clean effectively and can even cause vehicle damage.
- Environment – Whether it’s coastal, mountains, foothills, salty atmosphere, lots of road salt/brine, sand, clay, or grit, environmental factors need to be considered when maintaining and adjusting your equipment and chemicals.
- Cleaning – It’s also important to keep equipment clean, particularly components close to the floor, as buildup of sludge and grime can hide equipment issues and even contribute to premature wear or failure. This is particularly true of the conveyor and its parts, seals, slides, cylinders, chain, and pushers. The conveyor can be one of the most neglected components in the tunnel, as most of it is hidden in the conveyor trench.
- The conveyor trench can also become a catch-all for anything and everything, not just sludge and grime. Keeping the trench clean can extend the life not only of the conveyor itself and its parts but also of other components in the tunnel. Remember that reclaim systems use the trench to capture water used in the tunnel, returning it for processing and reuse. Regularly cleaning the trench will prevent buildup of muck throughout the tunnel and help keep the whole system healthy and running for years to come.
- Type of chemicals, or lack thereof – Be aware of chemical situations that can attack metal parts, as well as of underutilizing chemicals to properly lubricate brushes. Using the proper type and amount of chemicals helps equipment operate at its best.
- Brush pressures – Adjust air cylinders and equipment stops for proper penetration and over-travel.
- Brush speeds – Make adjustments related to new equipment break-in and track speed.
- Worn bearings – These can prevent brushes from moving freely.
- Switches – These include photo eyes, proximity switches (roller location, pulse), sonars, loops, and loop pads.
- Equipment speed is important to make sure it’s not stressed to the point of premature wear or breakage.
- On-line anti-collision devices - While these devices cannot totally replace employee training and eliminate all claims, they can be a useful tool in reducing them. You will need to make them part of your maintenance plan and test them daily to ensure they are functioning properly when needed.
In summary:
- Inspect your <strong>equipment</strong>, chemicals, and operation daily; and engage a monthly or quarterly preventive maintenance plan with your equipment supplier.
- Train and retrain your <strong>employees</strong> to observe equipment, properly instruct and guide customers, look for preexisting damage, and know which vehicles are susceptible to damage.
- Explicitly instruct <strong>customers</strong> on use of your car wash using as many methods as possible, including verbal guidance, menus, instructional and directional signage, and lighting.
Call on the experienced service team at Howco to be your guide and partner in keeping your car wash well-maintained and damage-free.
Related Resources
What are you waiting for?
Take the first step toward your business goals and reach out today. Our team is ready to get started when you are.