Don’t Neglect Your Routine Maintenance
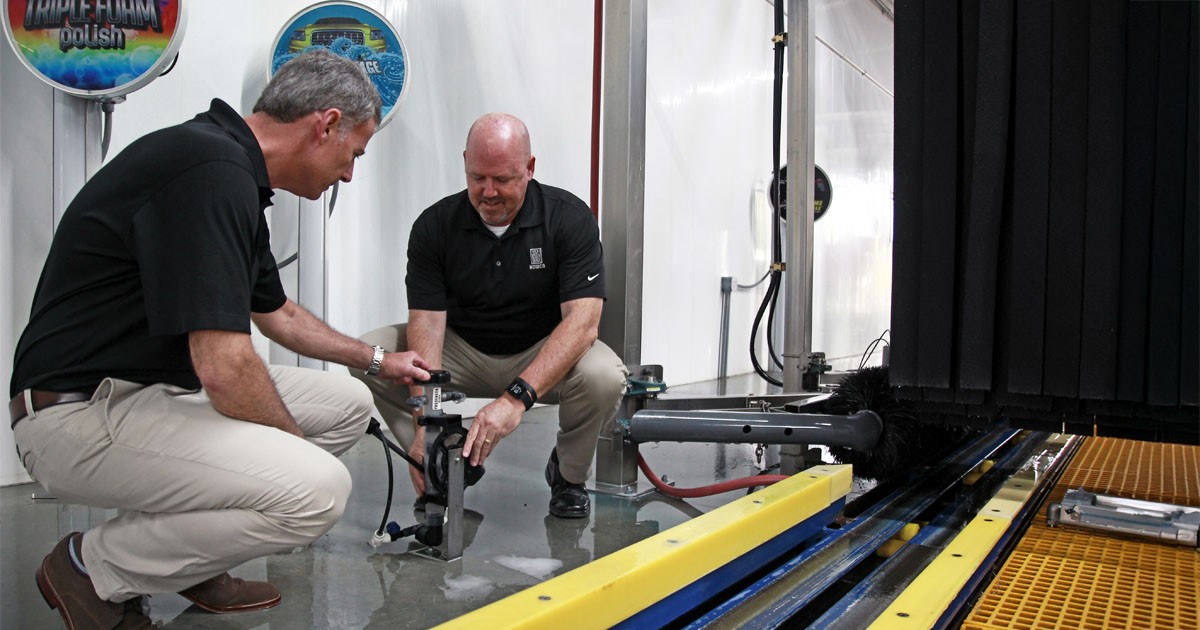
Ensure Employee and Customer Safety with Preventive Maintenance, Proper Training, and Diligent Housekeeping
by Howco Safety, Health, & Risk Management Team
Most car wash operators are keenly aware of the critical importance and value of regular car wash equipment maintenance. Often operators engage in monthly or quarterly preventive maintenance (PM) programs that can detect a variety of issues and provide a qualified and experienced set of eyes and ears to do so. A regular PM program keeps equipment functioning as it should and helps prevent downtime and lost revenue.
Why have a Preventive Maintenance Program?
What might not occur to some operators is that PM can also help detect and prevent potential safety issues for employees and customers. Like any industrial setting, a car wash location often has:
- continually moving equipment
- hydraulic and/or pneumatic systems
- electrical components
- chemical use and storage
- vacuum hoses
- excessive tire gloss accumulation and spills
- extension cords
- slippery public area floors and lots
- ignored restrooms
- and numerous other elements can all provide unwanted safety issues if they are not properly maintained and/or monitored.
Our best advice is to prevent safety issues before they happen. Having trained professionals regularly observe and maintain your equipment is the single best thing operators can do to prevent injuries. By having a PM program, you can shield unqualified and/or inexperienced employees from having to tackle potentially hazardous situations. A conveyor is generally the most dangerous component of a car wash, and keeping non-professional personnel from attempting to diagnose and repair it is strongly recommended.
Routine Housekeeping
Another form of preventive maintenance important to the safe operation of a car wash is housekeeping. Not only does maintaining a clean and orderly building and lot help ensure efficient operations, but it also helps protect both employees and customers. Well-maintained equipment rooms, vehicle tunnels, hallways, lobbies, and restrooms ensure walking and work surfaces are free of trash, clutter, and slipping hazards. Properly trained employees who execute your operational standards correctly are the best prevention for most mishaps.
By making housekeeping a priority, operators are able to use equipment rooms and tunnels as designed and provide access to equipment such as electrical panels and other machinery without any hazards present. Housekeeping attention to detail also ensures employees and customers a safe environment in public areas.
Make sure you hit every spot
Lastly, a well-maintained detail/finishing area prevents the clutter of vacuum hoses and trash as well as accumulation of tire gloss on walking surfaces, thereby presenting a professional image that should be the goal of all wash operators.
With few unusual exceptions, most safety issues can be prevented with an ongoing preventive maintenance program, diligent housekeeping, proper and continuous employee training, and a good dose of common sense. Talk to our team today to explore a PM program for your wash.
Related Resources
What are you waiting for?
Take the first step toward your business goals and reach out today. Our team is ready to get started when you are.